Basic Concept of Stretch Ratio
First, let's demystify the term "stretch ratio. What is the stretch ratio? It refers to the proportion of the length change of the material under the action of an external force, specifically the maximum extension from the original state to the fracture. Understanding this is crucial for us to grasp material behavior. By comparing the performance of different types of materials (such as metals, plastics and composites), we can better understand their respective characteristics and potential uses.
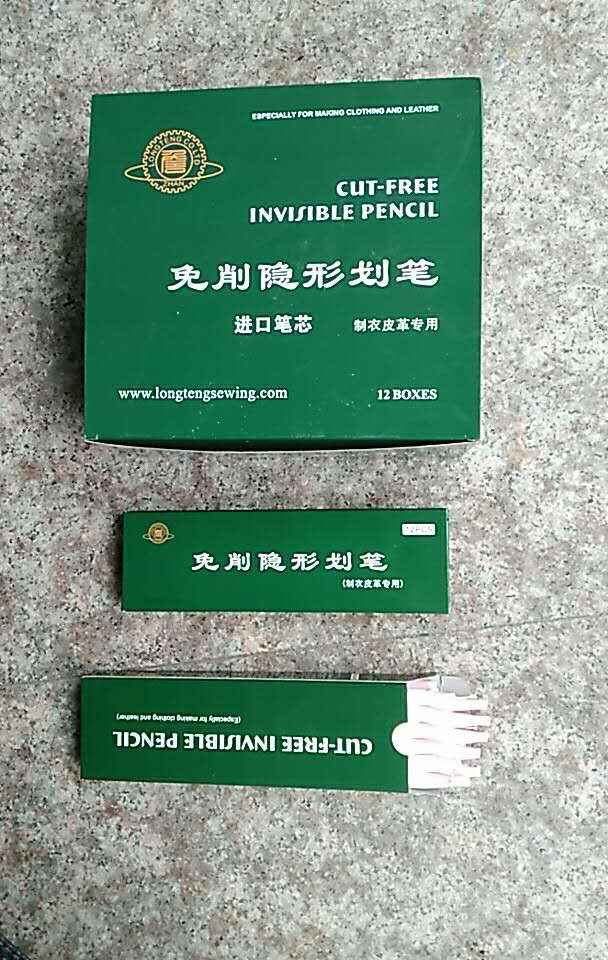
For example, some metal alloys are known for their excellent toughness and are able to recover even when subjected to extreme pressure, while other polymers, although initially rigid, exhibit amazing recovery after moderate deformation. The unique properties of each substance determine its scope of application-from building structures to electronic product housings, all dependent on sound material selection decisions.
Why Stretch Ratio is Important
In the engineering field and other manufacturing industries, accurate measurement and deep understanding of the stretch ratio is an indispensable part. This is because the stretch ratio directly affects the safety and durability of the product. A high stretch ratio means better flexibility and greater energy absorption, which is especially critical for applications that must cope with extreme conditions. Vice versa, if a material exhibits a very low stretch ratio, it is implied that it is relatively fragile and prone to breakage or failure.
Considering these problems, paying full attention to the stretch ratio factor in the early stage of design can prevent many possible problems in the later stage and ensure the stable and reliable quality of the final product. For example, lightweight, high-strength titanium alloys used in the aerospace industry perform well in harsh environments due to their excellent mechanical properties; household appliance manufacturers also carefully select rubber seals with the right elasticity to ensure that leakage does not occur during long-term use.
Real Tensile Test Process
Next, let's walk into the laboratory together and experience for ourselves how the tensile test is carried out in actual operation! From sample preparation to loading device setting, to data collection and analysis, each step requires strict precision control to draw reliable conclusions. The experimenter adjusts the parameter settings according to the specific nature of the sample to be tested, such as the application rate, ambient temperature and humidity and other variables, to simulate the change trend of the material under real-world conditions.
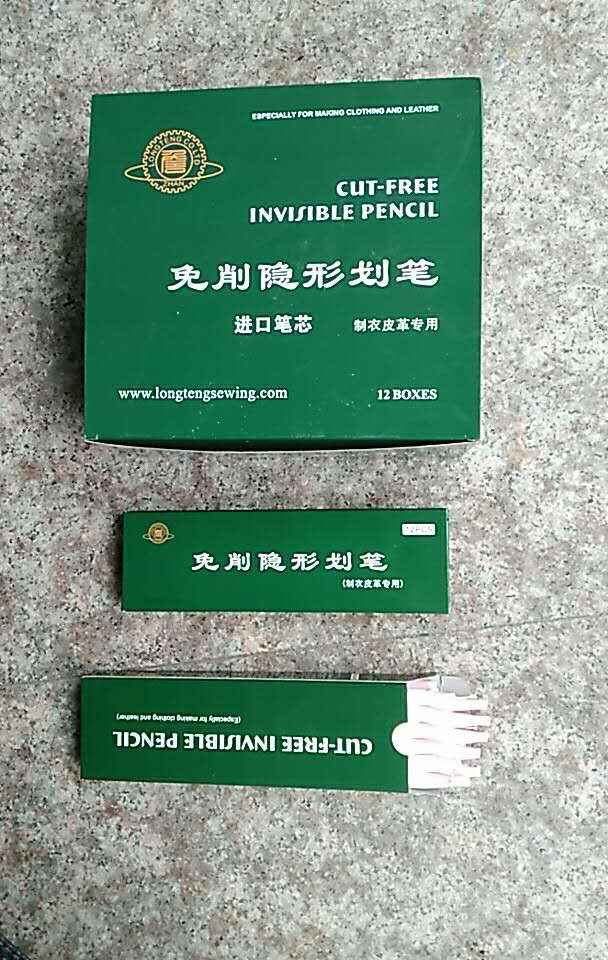
However, there are many difficulties to overcome in this process. For example, for very soft or extremely hard materials, improper fixing of the fixture may cause the specimen to slip or even destroy in advance; temperature fluctuations may also cause problems such as reading deviation. In the face of the above challenges, scientists continue to innovate and improve technology and methodology, and strive to maximize the restoration of the actual situation of the mechanical response phenomenon.
Explaining the secret of stretch curves
Once the full tensile test is completed, the corresponding stress-strain curve should be drawn immediately. This is an extremely important graphical tool for measuring material performance and one of the key reference sources for engineers to predict product performance. This chart contains many valuable information points, such as yield strength, elastic limit values, and the shaping interval until the final rupture termination point. Through the detailed analysis of these features, we can develop a more accurate and effective design for the development of new products.
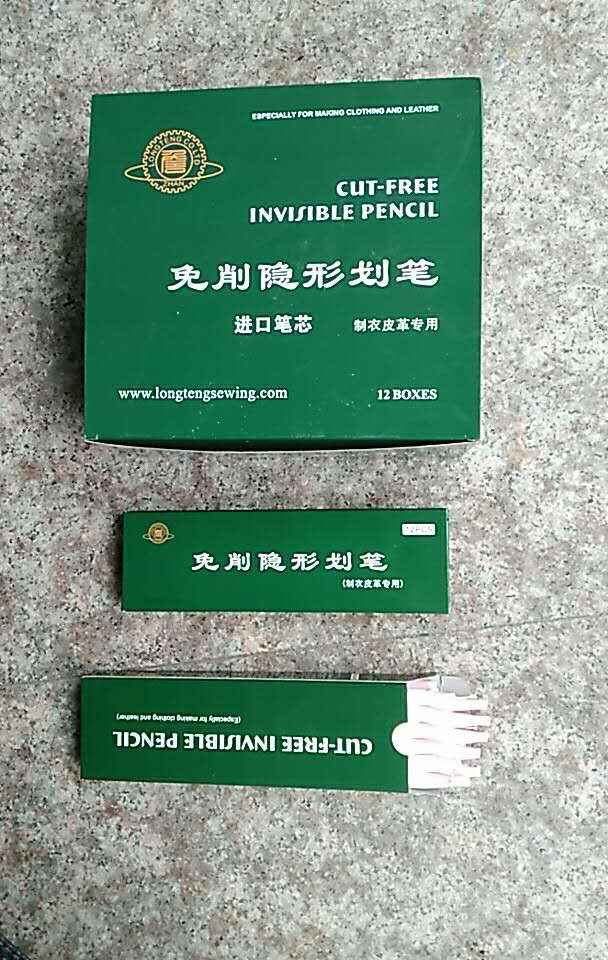
It is worth noting that the shape of the tensile curve formed by different types of materials is significantly different. Some show a clear bimodal or multi-peak distribution pattern, reflecting the complex microstructure structure, while others show a flat transition gradual monotonic increase pattern. No matter what kind of situation, can provide us with more clues about the nature of the material.
Choosing the right material: practical considerations based on stretch ratio
The last but most important task is to select the most appropriate technical solution in the context of the given project. Whether you are involved in large-scale infrastructure construction or small-scale handicraft production, a correct evaluation of the tensile properties of the required raw materials can help reduce uncertainty and increase work efficiency. This article will give several typical application scenarios in the selection of guidance, covering auto parts manufacturing, sports fitness equipment production and even daily household goods and other aspects.
according to the demand characteristics of the automobile industry, steel with good forgeability and weldability is selected as the main component of the body frame. For the body protection equipment that athletes often contact with collisions, priority is given to those man-made fiber fabrics that are both tough and have certain cushioning effect. As for frequently held objects such as kitchen knife handles, wooden materials that feel comfortable and are not easy to wear and crack tend to be used. In summary, a combination of factors weighing the pros and cons to make the best choice is an effective way to achieve the desired results.